When considering the incorpПloration of a 200,000 kcal/h thermal oil boiler into your industrial process, understanding the intricacies of its operation and benefits is crucial. This type of boiler serves a pivotal role in various sectors including the chemical, food, textile, and petrochemical industries. Its implementation can result in significant enhancements in efficiency, safety, and operation control.
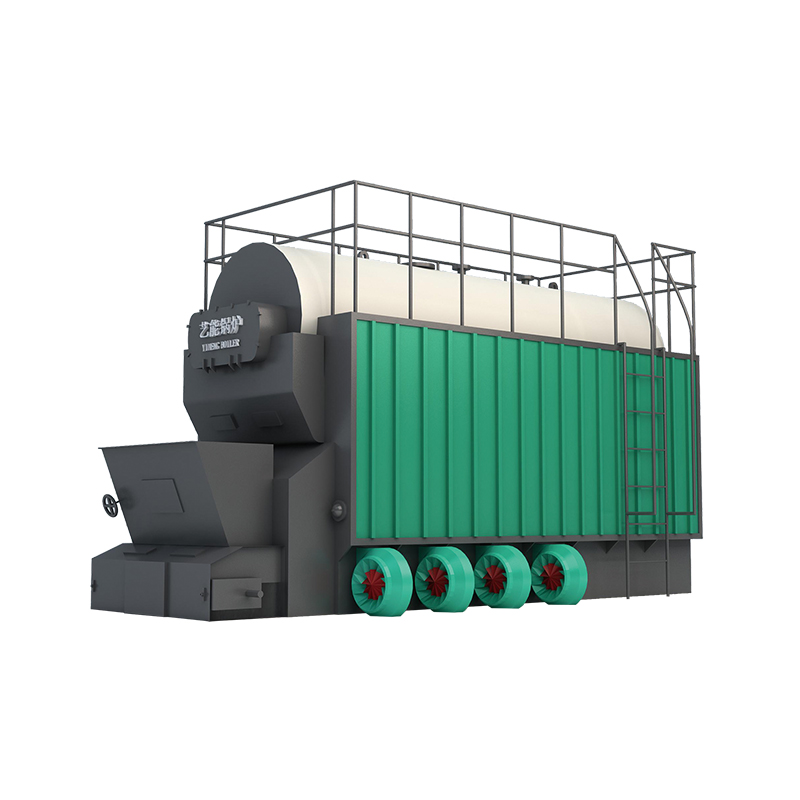
One of the standout advantages of a 200,000 kcal/h thermal oil boiler is its high degree of efficiency, achieved by transferring heat indirectly through a liquid medium instead of directly involving steam or water. This not only lowers the operational pressure but also minimizes the risk of corrosion and scaling, which are common issues in traditional steam boilers. Given these factors, thermal oil systems sustain longer lifespans, reducing the frequency of maintenance and downtime, which contributes to operational cost savings in the long run.
From a safety perspective,
thermal oil boilers operate at significantly lower pressures. This inherently makes them safer than high-pressure steam systems, minimizing the risk of explosions and related hazards. Furthermore, modern thermal oil boilers come equipped with a range of safety features, including temperature control systems, pressure relief valves, and automatic shutdown mechanisms. These features ensure compliance with safety regulations and offer peace of mind in managing sensitive industrial processes.
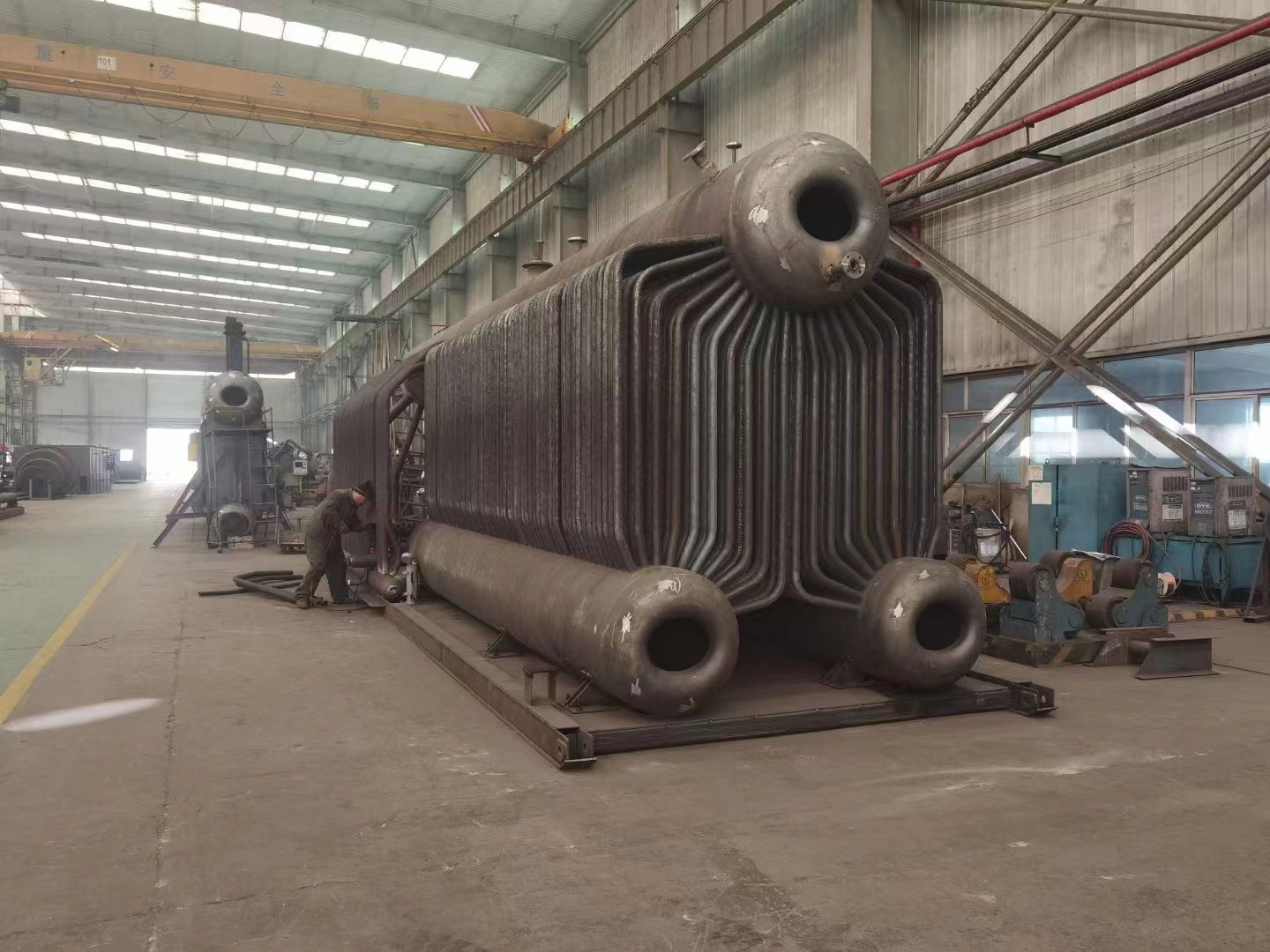
Efficiency and safety aside, the precise control offered by thermal oil boilers plays a critical role in complex industrial applications. By maintaining stable temperatures with minimal fluctuations, these boilers enable refined control over processes that demand stringent thermal conditions. For industries reliant on accuracy, such as pharmaceuticals or food production, the ability to maintain consistent thermal input can significantly enhance product quality and yield.
The adoption of a 200,000 kcal/h thermal oil boiler also brings with it the advantage of fuel flexibility. These systems can be engineered to operate using different types of fuels, including natural gas, heavy oil, or even biomass, providing industries with the flexibility to adapt to changing fuel availability and cost dynamics. In an era increasingly dominated by energy considerations, this adaptability can prove critical in aligning operational goals with sustainable practices.
200,000 kcal/h thermal oil boiler
In terms of energy consumption, optimizing a 200,000 kcal/h thermal oil boiler involves leveraging technologies that enhance heat recovery and insulation. Modern systems often utilize economizers to capture waste heat from exhaust gases, translating to improved overall system efficiency. Additionally, employing advanced insulation materials reduces heat loss, further minimizing energy consumption and carbon footprint.
Incorporating user-friendly features such as automated systems and digital controls is another notable trend in enhancing the EAT metrics of thermal oil boilers. Automation facilitates continuous operation without the need for constant supervision, freeing up human resources for other tasks within the facility. Meanwhile, digital controls allow for remote monitoring and adjustments, paving the way for predictive maintenance and minimizing unplanned downtime.
Expert recommendations underscore the importance of regular maintenance and inspections, as even the most sophisticated thermal oil boilers require routine checks to maintain optimal performance. This includes monitoring the thermal fluid quality, inspecting the combustion chamber, and verifying the effectiveness of safety devices. By adhering to a consistent maintenance schedule, operators not only enhance the longevity of the system but also foster a culture of reliability and safety that is indispensable in modern industrial environments.
Authoritative insights indicate that selecting the right thermal oil, tailored to the specific application requirements, is crucial. The oil's thermal stability, viscosity, and chemical composition can significantly impact the overall system efficiency and safety. Consulting with thermal fluid experts and leveraging dedicated analysis tools can offer invaluable guidance in making informed decisions tailored to your operational needs.
In conclusion, investing in a 200,000 kcal/h thermal oil boiler entails a detailed understanding of its operational dynamics, safety benefits, and efficiency potential. Such a system aligns well with the principles of Expertise, Authoritativeness, and Trustworthiness by ensuring high-performance standards, conforming to safety protocols, and enhancing operational reliability. By integrating cutting-edge technology with expert maintenance practices, industries can achieve a significant edge in their production capabilities.