Navigating the industrial landscape, one cannot overlook the pivotal role of the steam boiler economizer in enhancing energy efficiency. This critical component captures waste heat from boiler exhaust gases and repurposes it to preheat the boiler's incoming water supply. Incorporating an economizer into your steam boiler system is an investment that yields substantial returns in terms of energy conservation and operational efficiency.
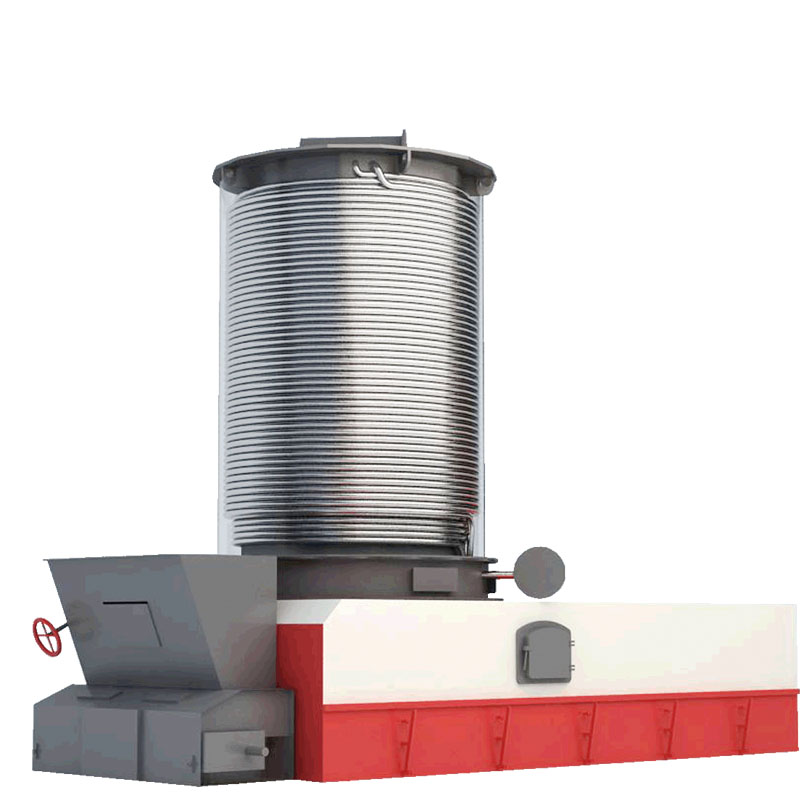
Imagine a bustling manufacturing plant where energy demands are relentless. Here, economizers fit seamlessly, delivering reduced fuel consumption by harnessing otherwise wasted heat. This translates to significant cost savings, a reduction in greenhouse gas emissions, and optimized resource utilization. For every ton of fuel saved, carbon footprints diminish considerably, aligning operations with global sustainability standards.
The expertise behind steam boiler economizers is rooted in thermodynamics and mechanical engineering. These devices are intricately designed to withstand high-temperature environments and corrosive conditions typical of steam production processes. Engineers meticulously select materials such as stainless steel and employ advanced coatings to extend the economizer's lifespan and enhance its thermal conductivity. As a result, economizers promise durability and reliable performance.
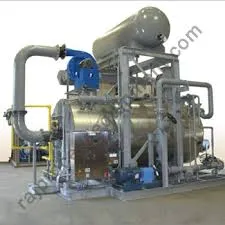
Real-world applications abound, showcasing the efficacy of economizers across various industries. One prominent example is chemical manufacturing, where heat recovery steam generators incorporate economizers to efficiently handle cyclical demands for both steam and electricity. This dual-purpose approach underscores the versatility of economizers, making them indispensable in sectors requiring copious amounts of steam and power.
Industry accreditation further adds to the authority of these devices. Regulatory bodies govern the implementation of economizers, ensuring safety and performance compliance. Manufacturers adhere to stringent guidelines set forth by organizations like the American Society of Mechanical Engineers (ASME). These standards affirm the quality and reliability of economizers, providing assurance to stakeholders and cementing trustworthiness.
steam boiler economizer
Retrofitting existing boiler systems with economizers is another avenue for energy optimization. The transition involves careful evaluation and integration by seasoned professionals to tailor solutions that maximize heat recovery based on specific system configurations. Such projects underscore the adaptability of economizers in improving the energy efficiency of legacy systems, fulfilling both economic and environmental objectives.
Moreover, the digital transformation of industrial operations contributes to the rise of smart economizers. These cutting-edge versions are integrated with IoT technologies, enabling real-time monitoring and predictive maintenance. By utilizing data analytics, operators can make informed decisions that enhance operational efficiency and preempt potential failures, thus reinforcing the trust in economizers as resilient components of modern energy systems.
A significant factor influencing the successful integration of economizers is stakeholder collaboration. Facility managers, engineers, and financial planners must work in concert to ensure the economizer selection aligns with organizational goals. This collaborative approach fosters a holistic view of energy management, emphasizing the importance of economizers in pursuing long-term sustainability targets.
To wrap it up, the steam boiler economizer is more than just an add-on; it is a cornerstone of energy strategy. Embracing this technology unlocks multiple benefits that extend beyond the immediate cost savings. It secures a proactive stance in responsible energy consumption, aligns operations with eco-friendly practices, and harnesses technological innovations to pave the way for future advancements in steam generation efficiency.