In the competitive world of metal processing, the role of high-quality boilers cannot be understated. As integral components, they ensure precise temperature control and efficient heat transfer, thereby influencing production times, product quality, and energy consumption. Understanding the intricacies of selecting the right boiler can significantly enhance operational efficiency and profitability.
Here is a comprehensive exploration of what makes a high-quality boiler indispensable for metal processing facilities.
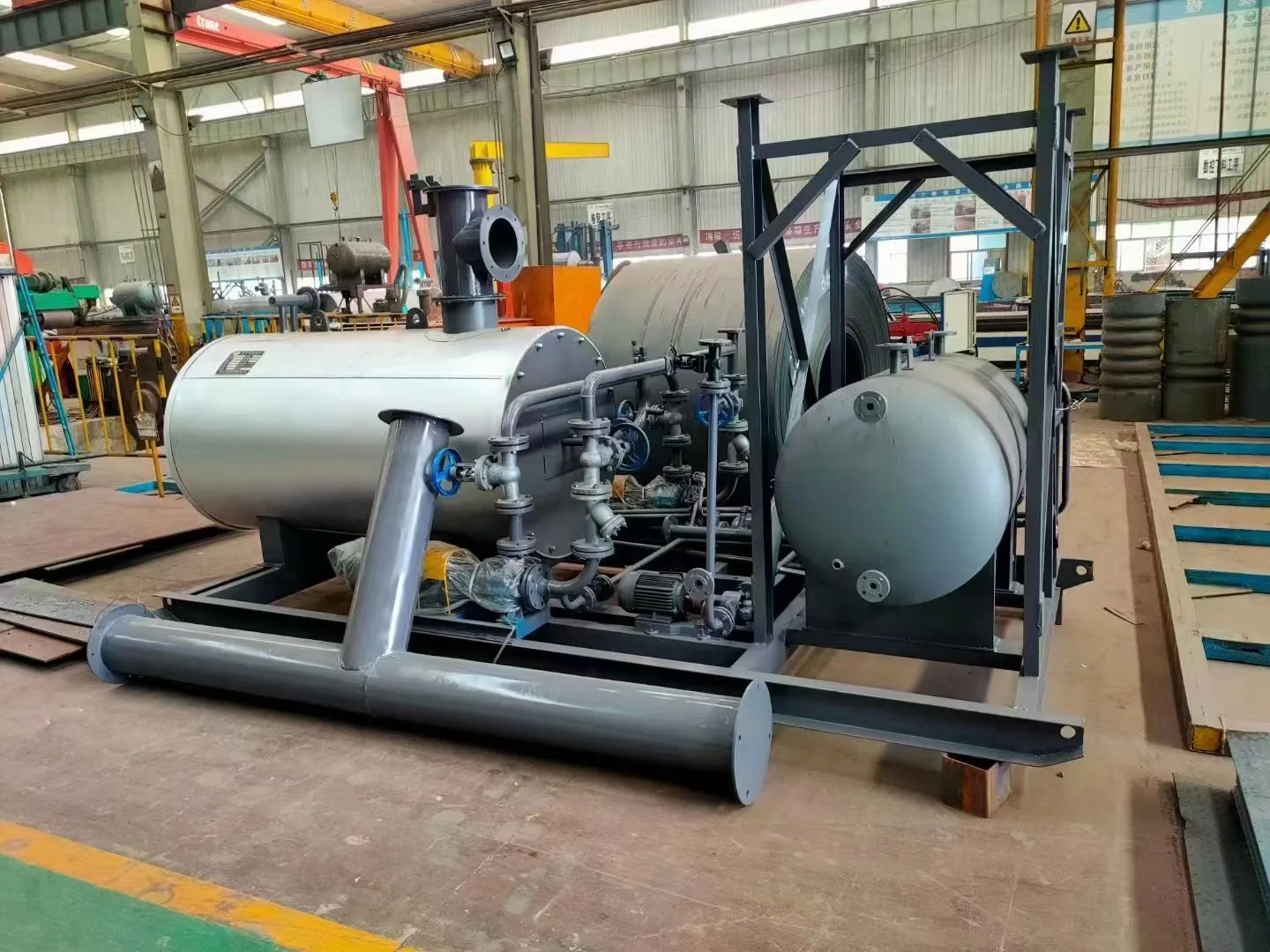
The first aspect to consider when evaluating boilers for metal processing is their build quality and reliability. A high-quality boiler is constructed from durable materials that withstand the rigors of intense heat and pressure. Advanced models are often crafted from high-grade stainless steel and incorporate cutting-edge welding techniques to enhance durability. By ensuring longevity and minimizing the frequency of maintenance, these boilers offer a significant return on investment.
Equally important is the precision in temperature control. The quality of metal processing is largely dependent on maintaining specific temperatures tailored to different metals and desired outcomes. High-quality boilers are equipped with state-of-the-art temperature control systems that allow for precise adjustments. These systems utilize advanced sensors and digital control interfaces, providing users with real-time monitoring and adjustments. This precision not only enhances the quality of the metal products but also reduces energy consumption and operational costs.
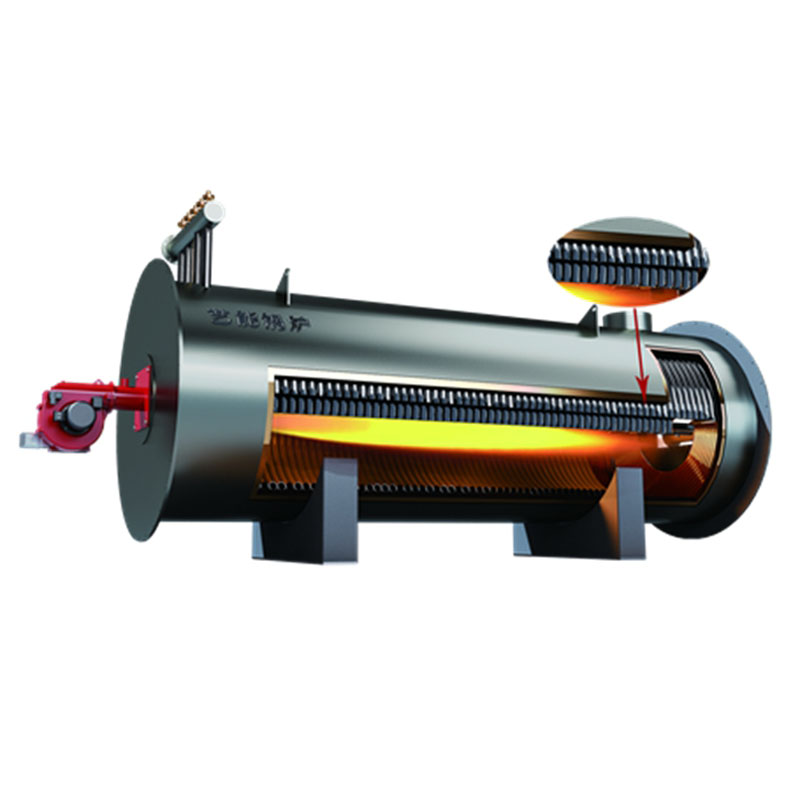
Energy efficiency is another crucial feature of high-quality boilers. As energy prices continue to soar, manufacturers are increasingly prioritizing boilers that optimize fuel usage without compromising performance. Efficient boilers adopt technologies such as condensing heat exchangers and intelligent control systems to maximize the energy extracted from fuel. This reduces waste and emissions, aligning with the growing emphasis on sustainable manufacturing practices.
Safety features are paramount in the design of a high-quality boiler. Modern models incorporate multiple safety mechanisms, including automatic shut-off systems, pressure release valves, and robust sealing technologies. These features are designed to prevent accidents and ensure safe operation, even under the most demanding conditions. Trustworthiness in a boiler’s safety protocols not only protects personnel but also secures expensive equipment and materials from potential damage.
high quality boiler for metal processing
High-quality boilers also exemplify technical expertise through their integration with Industry 4.0 technologies. The trend towards smart manufacturing has led to the development of boilers equipped with IoT connectivity and remote monitoring capabilities. These features enable operators to gather comprehensive data on the boiler’s performance, thus facilitating predictive maintenance and reducing downtime. The integration of AI-driven analytics helps identify efficiency tweaks and anticipate potential issues before they escalate, enhancing overall operational effectiveness.
Furthermore, expert manufacturers of high-quality boilers offer comprehensive support services, ranging from installation guidance to ongoing maintenance and emergency repairs. This support network is a testament to the manufacturer’s commitment to customer satisfaction and the boiler’s reliable performance. Collaboration with seasoned technicians ensures that any operational hiccups are swiftly managed, which is crucial for maintaining continuity in metal processing operations.
Additionally, certification from established industry bodies and compliance with international standards such as ASME (American Society of Mechanical Engineers) or CE marking (Conformité Européenne) is a clear indicator of a boiler’s authority and reliability. Such certifications guarantee that the boiler meets rigorous safety and performance benchmarks, enhancing trust and confidence among users.
In summary, selecting a high-quality boiler for metal processing involves careful consideration of multiple factors including durability, precision, energy efficiency, and safety. By opting for a boiler that embodies these qualities, businesses not only enhance their production capabilities but also achieve significant cost savings and environmental benefits. A high-quality boiler positions a metal processing facility at the forefront of technological innovation, ensuring sustained competitiveness and growth in the evolving industrial landscape. This adherence to excellence underscores the boiler’s role as not just a tool, but as a pivotal partner in achieving operational success.