When considering the operational and safety standards of industrial systems, the hot oil pump emerges as a crucial component. The role of a hot oil pump in thermal oil systems is paramount, as it facilitates the movement of heat transfer fluids. This ensures that the system maintains its efficiency and reliability.
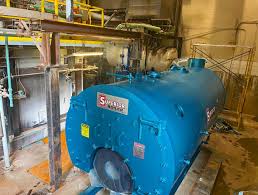
A hot oil pump, designed specifically for high-temperature applications, is essential in maintaining seamless processes within industries such as chemical processing, food production, and manufacturing. The ability of these pumps to operate at elevated temperatures without degrading ensures that operations remain uninterrupted, which is a primary concern for industries that rely heavily on consistent thermal processes.
Experience within the industry showcases the versatility and adaptability of hot oil pumps. For instance, a leading chemical processing plant switched from a conventional pump to a modern hot oil pump and noted an appreciable increase in efficiency. Not only did the new pump withstand the challenging conditions of high temperatures, but it also reduced maintenance costs significantly due to its robust design. This shift underscores the importance of selecting specific equipment tailored to high-temperature needs.
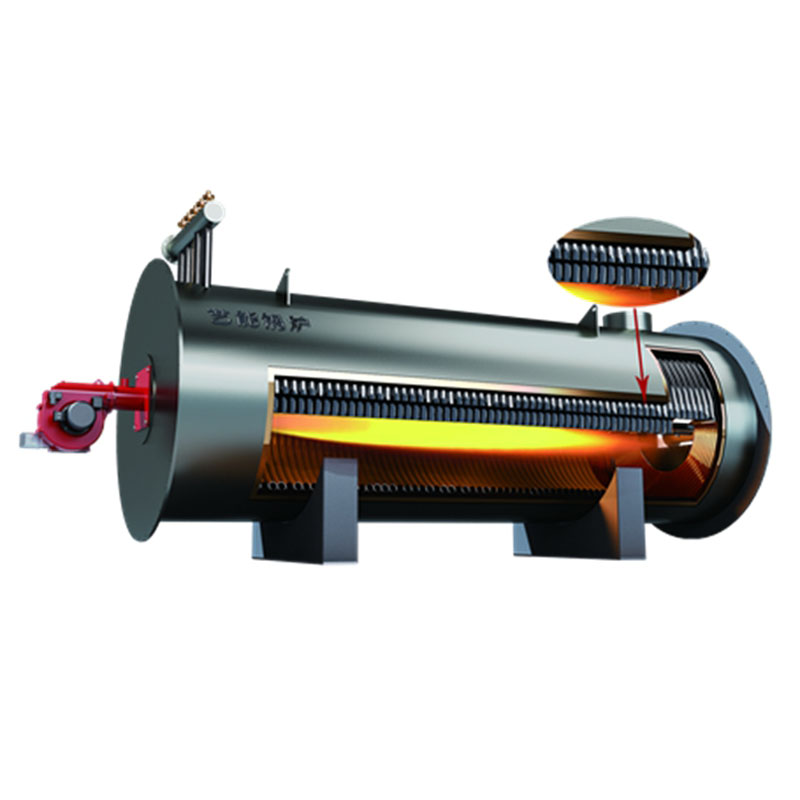
From an expertise perspective, understanding the construction and material composition of hot oil pumps is essential for their optimal application. These pumps are typically constructed from alloys and materials that can withstand thermal expansion and the corrosive nature of some heat transfer fluids. Engineers often recommend using pumps with mechanical seals designed to handle the thermal stresses associated with high-temperature fluids. Furthermore, the pump's ability to sustain a high flow rate without fluctuation is crucial for industries that require precise thermal management.
hot oil pump
The authoritativeness of a hot oil pump is further reinforced by its widespread use across various sectors worldwide. Industrial experts often cite these pumps in papers and guidelines focused on the optimization of thermal systems. For a piece of equipment to become an industry standard, it must undergo rigorous testing and continuous improvements, ensuring it meets international safety and performance criteria.
This showcases a track record of reliability and efficiency.
Trustworthiness is a significant factor, particularly when safety is a concern in high-temperature operations. A hot oil pump is not merely functional equipment but a critical safety component within an industrial system. Quality manufacturers often subject these pumps to extensive quality control processes to ensure their reliability. Trust is built through transparency; manufacturers often provide detailed documentation on the specification, testing, and maintenance of their pumps.
The selection of a suitable hot oil pump is multilayered, involving precise calculations regarding the required flow rate, pressure, and temperature ranges. Professional consultation with engineers who specialize in thermal systems can provide invaluable insights into the most appropriate pump for a given application. In instances where the incorrect pump type has been chosen, the result is often unnecessary downtime and inflated operational costs, emphasizing the need for expertise in selection.
In conclusion, the hot oil pump is indispensable within any thermal system requiring the efficient and safe transfer of high-temperature fluids. With real-world experience demonstrating their tangible benefits, strong expertise underpinning their design and application, authoritative industry adoption, and the trustworthy reliability they offer, these pumps set the benchmark for performance and safety in demanding conditions. Whether it's for a new system installation or an upgrade of an existing one, hot oil pumps empower industries to achieve optimal thermal management, safeguarding their processes and ensuring the continuity of operations.