Understanding the pivotal role of steam boilers in autoclaves can be transformative for industries dependent on high-quality sterilization, material curing, or composite bonding. Steam boilers are integral components providing the essential heat source required for the efficacy of autoclaves. Precision, reliability, and expertise in the utilization of steam boilers for autoclave operations can significantly impact productivity, safety, and economic efficiency across diverse sectors from manufacturing to healthcare.
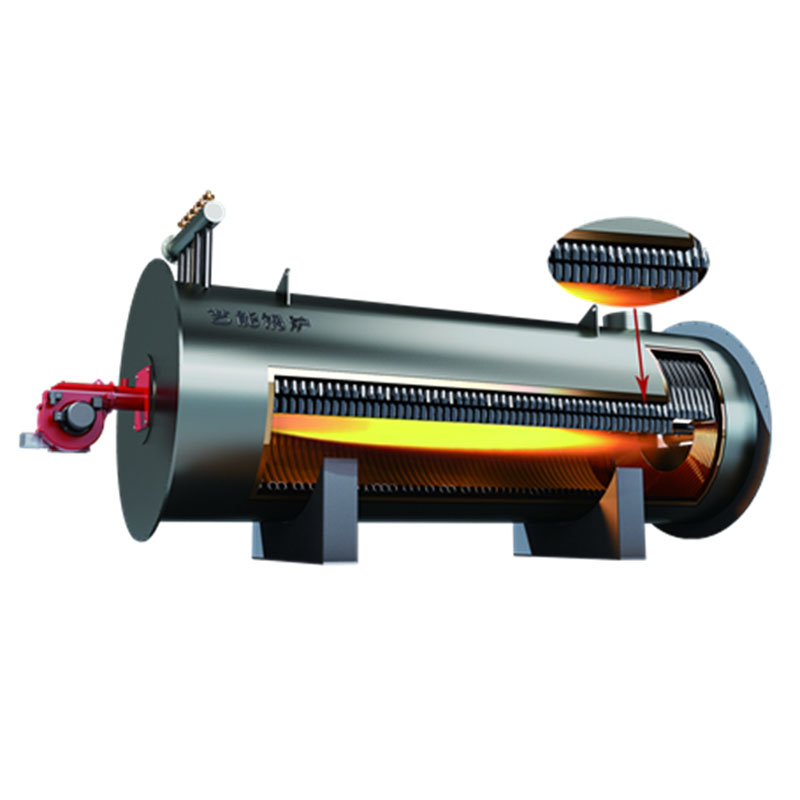
At the heart of this relationship is the steam boiler's ability to generate consistent and controlled steam at the required pressure and temperature, ensuring that the autoclave's load is uniformly sterilized or cured. Steam boilers feed the autoclave cylinders with steam, maintaining an environment ideal for destroying harmful bacteria or facilitating the proper curing of materials. Selecting the right boiler necessitates a sophisticated understanding of the type of load, cycle times, volume capacity, and energy efficiency.
Industries such as medical device manufacturing and food processing rely heavily on autoclaves paired with advanced steam boilers. In these fields, compliance with stringent regulatory standards like those from the FDA or ISO underscore the importance of a trustworthy and authoritative steam supply system. Any deviation from precise operating conditions can result in inadequate sterilization, leading to potential product recalls or safety breaches.
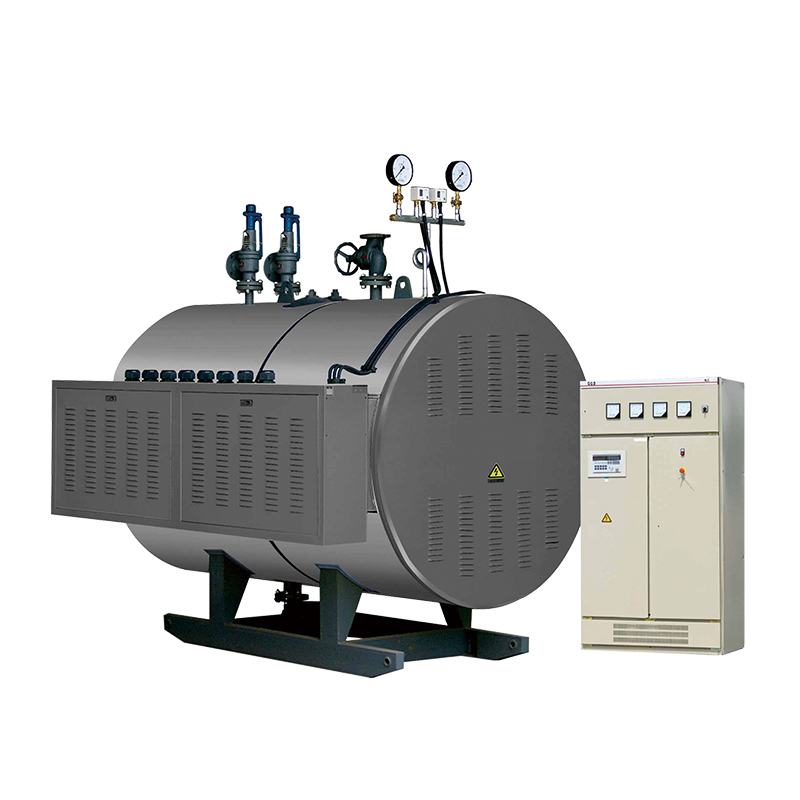
The expertise required in managing steam boilers goes beyond mere operation. It includes routine maintenance checks to prevent scale buildup, which can lead to inefficient heat transfer and increased energy consumption. Technicians should employ regular water chemistry tests to safeguard the boiler's integrity, ensuring that steam quality is never compromised. Boilers of advanced design now incorporate smart technologies that automate these processes and provide real-time diagnostics for preventive maintenance.
steam boiler for autoclave
Experience dictates that the choice of materials used in constructing steam boilers is crucial. High-performance steel alloys, resistant to corrosion and high pressures, extend the longevity and resilience of the boiler systems. This choice reflects both expertise and authoritativeness in ensuring reliability under continuous operation.
A dramatic evolution is underway in steam boiler technology, whereby eco-friendly solutions are increasingly becoming industry standards. Companies now seek boilers equipped with economizers to reclaim heat from exhaust gases, elevating their sustainability profile while reducing operational costs. Such boilers not only align with global climate initiatives but also serve as a trust-building mechanism within consumer bases sensitive to environmental stewardship.
Real-world operational case studies fortify the trustworthiness of implementing state-of-the-art steam boiler solutions. Automotive industries engaged in the fabrication of composite materials, for example, have reported notable improvements in cycle times and uniformity of results when leveraging modern steam boilers designed for optimal performance in high throughput environments.
In sum, the intricate interplay between steam boilers and autoclaves defines the credibility and success of numerous high-stakes applications. The journey from selecting a boiler, ensuring its proper maintenance, to evolving it with green technology outlines a rigorous pathway rooted in experience, expertise, authoritativeness, and trustworthiness. For industries aiming to retain a competitive edge and guarantee safety and compliance, embracing the next-generation steam boiler systems is not just advantageous but essential.