Waste heat boilers, often overlooked in the broader landscape of industrial equipment, are pivotal in enhancing energy efficiency across various sectors. These specialized boilers are designed to recover and utilize the excess heat generated during industrial processes and subsequently convert it into useful energy, thereby reducing operational costs and environmental impact.

In the dynamic world of industrial manufacturing, energy management is not just a cost-saving measure but a critical component of sustainable operations.
Waste heat boilers step into this role by acting as a conversion catalyst. They capture residual heat from flue gases or the exhaust of an industrial process and convert it into steam or hot water. This newfound energy source can serve numerous applications such as generating power in cogeneration plants, or providing process heating and industrial drying.
Expert users of waste heat boilers hail from industries like chemical manufacturing, refineries, and steel production, where high-temperature processes are routine. In these settings, waste heat boilers contribute substantially to energy conservation. For instance, in a chemical plant, the heat recovered from high-temperature reactors can feed a waste heat recovery unit attached to a boiler, which in turn drives turbines for electricity production or assists in other heat-based processes within the facility, significantly trimming energy consumption.
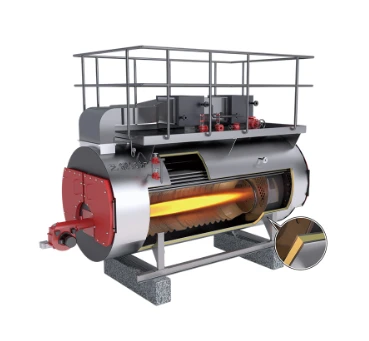
Technical expertise is critical when selecting and integrating a waste heat boiler into an industrial setup. The design and capacity of the boiler must align with the specific output of waste heat from the operation. Variations in process temperatures, flow rates, and the composition of exhaust gases necessitate a customized boiler solution. Such precision ensures optimal energy recovery and maximizes return on investment.
waste heat boiler
Authoritative guidance from specialized engineers can exponentially increase the efficiency of waste heat boilers. These professionals conduct thorough assessments of industrial processes and exhaust characteristics to recommend the most effective boiler types, whether it be fire-tube, water-tube, or a combination. They also provide strategic insights into maintaining system integrity, minimizing corrosion risks, and enhancing heat exchange efficiency.
Trustworthiness in waste heat boiler systems is cemented through robust performance metrics and reliability. Manufacturers often highlight their products' compliance with international standards like ASME and their certifications for safety and environmental management. Furthermore, long-term partnerships with clients for maintenance and training programs bolster trust and ensure the sustained performance of waste heat recovery installations.
In a corporate landscape where environmental accountability is as crucial as profitability, waste heat boilers present a win-win solution. By recycling energy that would otherwise dissipate as waste, industries not only enhance their bottom line but also contribute positively to reducing greenhouse gas emissions, aligning with global sustainability goals.
Thus, adopting waste heat boilers is not merely a nod to sustainable practices but a financially sound decision that leverages technical ingenuity and authoritative guidance for maximum benefit. As energy costs rise and environmental regulations tighten, the role of waste heat boilers in shaping efficient and responsible industrial operations is more important than ever.