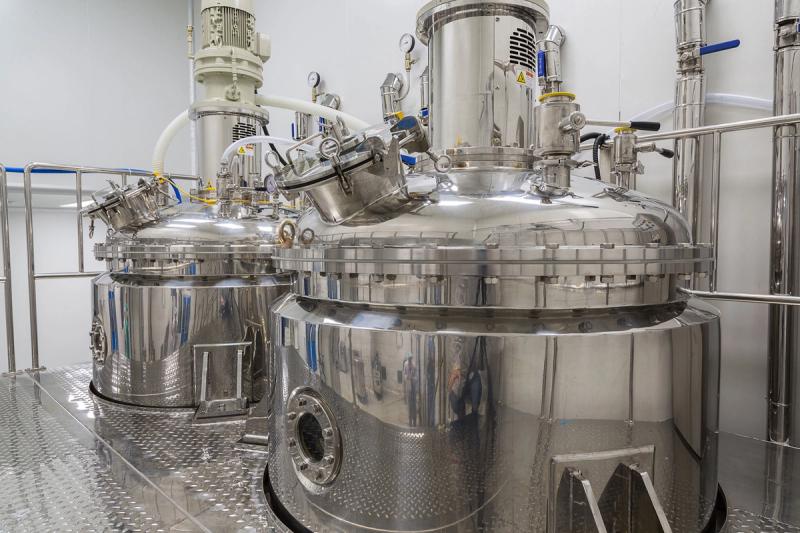
Today’s industrial companies are moving more of their manufacturing operations into automation and robotics — with new facilities and production lines designed to maximize space, as well as to reduce production time and labor costs. To meet this demand, the Commercial Boiler Industry is responding to thousands of companies who are moving to more technically advanced facilities or making the changes necessary to introduce the newer technologies in current plants.
Boilers are a key component of every heating system that provides warmth throughout entire manufacturing facilities. It is estimated that more than 60,000 industrial boilers exist in the US today with thousands of them needing to be updated. This need combined with the onslaught of automation and robotic manufacturing applications indicates the future holds many opportunities for the boiler manufacturing industry.
In this issue of EVERYTHING UNDER CONTROL, we will talk about the basics of what commercial boilers are, how they operate, and how new technology will affect the industry.
Industrial boilers today and tomorrow
Industrial boilers are used by all manufacturing industries — including automotive, major appliances, food and beverage, petrochemical, power, chemical and many more. Commercial office and multi-family buildings often use boilers for heating as well.
There are two types of boilers — one that produces hot water and one that produces steam, which is then used to carry out the heating process. The hot water or steam produced is transferred to all areas of the plant or commercial facility through a custom designed piping system.
In order to heat the water or produce the steam, boilers use different types of fuels — including both fossil and non-fossil — as well as biomass, which is carbon-based materials contained in living organisms. The water or steam enters radiators or other components that then disperse the heat needed to keep indoor spaces comfortable. Natural gas is the most common fuel used in commercial boilers. There are also other kinds of boilers available that burn fuel oil or use electric resistance coils to produce heating from electricity.

Some reported studies indicate that the US commercial boiler market is on pace to reach more than $1.5 billion by 2024 — and is expected to expand at a compound annual growth rate (CAGR) of nearly 5.0% from 2021 to 2028. The rapid move to automation and robotics throughout the manufacturing sector is expected to drive this growth in the US and global markets.
Many new boilers will be designed and manufactured to meet the needs of these companies that are moving manufacturing operations to more technically advanced facilities or making the changes necessary to introduce the newer technologies in current plants. In addition, there will be thousands of current boilers that will need to be replaced or upgraded with new technology as well.
Innovative boiler industry trends
During the past decade, a wide variety of innovative boiler industry trends have emerged at a rapid pace. As the demand for low NOx (Nitrogen Oxide) performance systems, higher efficiency units, and reduced carbon footprints increases, companies have access to the most cutting-edge and advanced systems ever designed with more innovations to come.
Low NOx boilers
Newly emerging low NOx regulations are designed to reduce the harmful effects of Nitrogen Oxide (NOx) gases on the environment. These reactive highly toxic gases are produced when fuel is combusted at high temperatures, such as with water heaters, boilers and furnaces.
Because of the harmful effects of NOx on the environment, a growing number of boiler manufacturers are working to get prepared for the coming regulations. In addition to lowered NOx and carbon monoxide emissions, the benefits of low NOx burners also include increased energy efficiency, improved product quality, reduced maintenance costs, and greater return on investment.
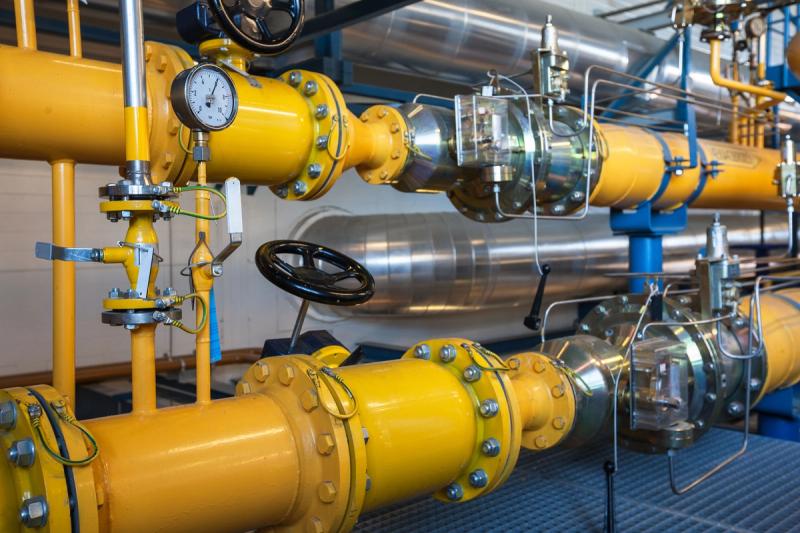
Packaged skid solution
A growing trend in process heating is the installation of ‘point-of-use’ steam or hot water generation equipment. In contrast to the central plant method, a smaller boiler system can deliver the needed energy transfer right at the process location. These smaller steam or hot water systems, often referred to as packaged skid solutions, are self-contained boiler plants.
A packaged boiler skid consists of a boiler, or multiple boilers, and the requisite accessories to complete steam or hot water generation and distribution. All essential equipment is packaged on a common skid base and is prepiped and wired during the manufacturing process at the builder’s facility, eliminating the need to perform these tasks at installation.
Many times, lengthy distribution piping in large facilities results in lost energy due to pressure drop, as well as radiation and convection losses. The self-contained, packaged boiler skid minimizes or eliminates this lengthy distribution and return piping or pumping requirements.
Another advantage of a packaged boiler skid is the ability to size the boiler system to match any specific process load. Many times, the compact footprint enables boiler plants to be located right on the factory floor. Facility owners may benefit from the flexibility and reduced capital investment provided by point-of-use boiler systems.
Coal or biomass fired DZL automatic chain grate steam boiler
Plug-and-play boiler installation
No longer are commercial boilers mammoth in size and made of cast iron. Many of today’s slimmer, more flexible, smaller units can be installed and transported with minimal effort. The mere compact size of today’s condensing boilers makes them easier to install, but many manufacturers are going a step further to make installation as simple as plug-and-play. Features like integrated low-loss headers work to streamline installation by significantly reducing the time required for system piping.
Blowdown systems
Today, boiler efficiency includes discussing water quality which can also have a critical impact on the lifespan of the hydronic system. As a result, manufacturers are beginning to focus more on packaged solutions that include blowdown systems that intentionally wastes water from a boiler to avoid the concentration of impurities during continuing evaporation of steam. The water is blown out of the boiler with some force by steam pressure within the boiler.
Water quality treatment
Water softener treatment systems eliminate scaling from forming in process equipment piping, as well as heat exchange systems. These solutions are also an effective way to bolster the effectiveness of rinsing and cleaning processes. Smaller boilers have narrower waterways and are more likely to become clogged or blocked with a combination of scale and magnetite. Blockages may affect the heat exchangers and circulators while coating the inner surface of the iron piping. Builders and installers are turning to the addition of water softener treatment systems as one of the steps taken to protect the health of the system by preventing buildup over time.
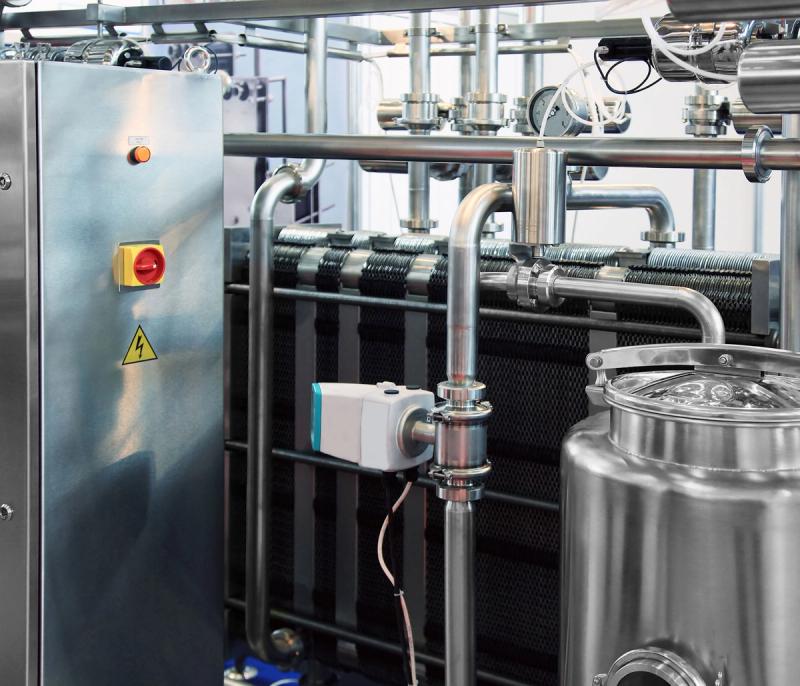
Industrial Internet of Things
The Industrial Internet of Things (IIoT) has impacted virtually every industry around the world and the boiler industry is no exception. Many boilers now offer some form of Wi-Fi capability with the ability to control the unit from virtually anywhere through an internet connection. The boiler industry can expect to see more progress in this area in the coming years. Companies will increasingly gain the ability to control and monitor their boiler from apps on their devices. Boiler manufacturers have also begun to use the IIoT to research new components to ensure customers have the most up to date systems available.
Remote monitoring
Remote monitoring provides an opportunity for users to be in control of their boiler 24 hours a day, even if they are not physically on-site. This technology has evolved over the years and today remote monitoring can be accomplished using any internet connected device. With the implementation of data-driven modems, many cybersecurity concerns associated with boiler management systems (BMS) being connected via the client’s server have been widely overcome.
Online computing services
- Platform as a Service (PaaS) is a category of cloud computing services that allows companies to provision, instantiate, run and manage a modular bundle comprising a computing platform and one or more applications. This can be accomplished without the complexity of building and maintaining the infrastructure typically associated with developing and launching the application(s) — and to allow developers to create, develop and package such software bundles.
- Software as a Service (SaaS) is a software distribution and licensing and delivery model in which software is licensed on a subscription basis and is centrally hosted. SaaS is sometimes referred to as “on-demand software.” A service provider gives customers access through the internet to applications that are developed and owned by the provider. This service allows each user to access programs via the internet instead of having to install the software on the user’s computer. Using SaaS gives users a greater degree of control and knowledge over their project and results in a more efficient and accurate system.
Electrical machine controls for over four decades
We are proud to have played an integral part in the operation and control of the many different types of automation and robotic manufacturing systems for the Commercial Boiler Industry.
We hope you have benefited from our latest issue of EVERYTHING UNDER CONTROL and have learned something you may not have known before. In future issues, we will provide you with information on the latest trends and advancements for a wide variety of industries that depend on c3controls products as an integral part of their machine controls.