What Is An Industrial Steam Boiler?
An industrial steam boiler serves as a crucial pressure vessel, generating steam by heating water and directing it through pipes to harness kinetic energy for diverse industrial applications.
Comprising essential components like a furnace, pot, tube bundle, flue, and control system, the industrial steam boiler operates cohesively. These elements collaborate systematically to collect and distribute the steam, generated through combustion, throughout various sectors of industrial production.
EPCB's industrial steam boiler stands out with distinctive advantages, including efficient energy conversion, customizable output temperature and pressure, operational adaptability, and reliability. Tailored to meet the diverse needs of different industries, these boilers play a pivotal role in advancing and sustaining modern industrial development.
The Working Principle Of Steam Boilers
There are various types of steam boilers, but they are all designed to produce steam for different industrial purposes. Here are the specific principles
- Fuel combustion and heat release: Various fuels, including coal, natural gas, and oil, are employed in industrial steam boilers. Ignition of the fuel within the furnace chamber initiates high-temperature combustion. Throughout this combustion process, the chemical energy contained in the fuel is liberated, transforming into heat energy. Consequently, flue gases and exhaust gases are generated and expelled through the flue system.
- Heating of water and conversion to steam: The heat energy liberated during combustion moves through the furnace chamber's wall casing, transferring to the adjacent tube bundles or directly to the pot barrel. This barrel, filled with water, undergoes a transfer of heat energy, resulting in its gradual heating. With increasing temperature, the water undergoes a phase change, transitioning into steam.
-
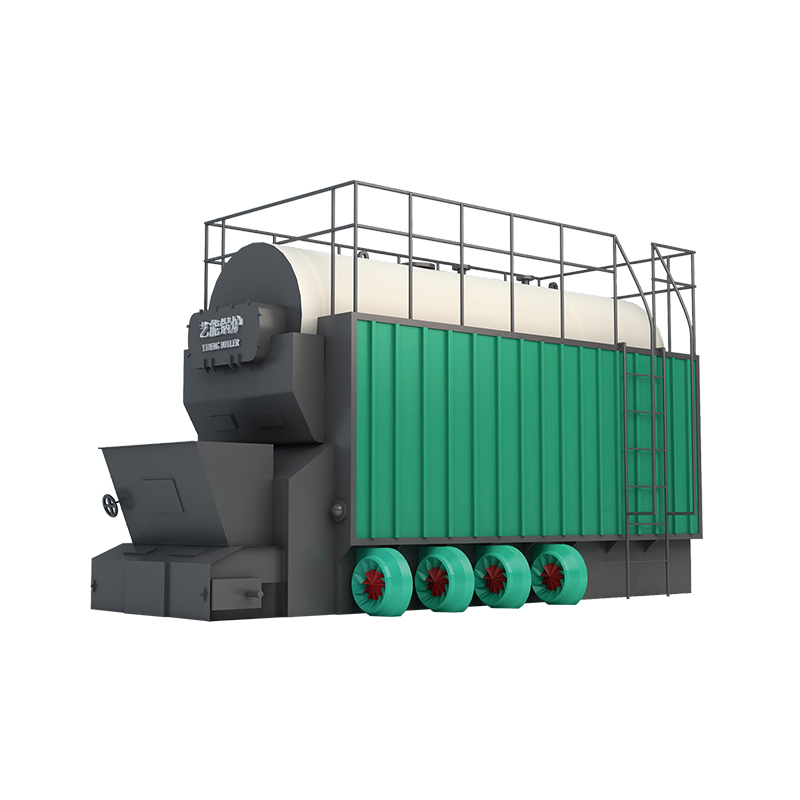
- Collection and distribution of steam: As the water undergoes heating, the generated steam accumulates within the pot's barrel. Once the steam attains the desired pressure and temperature, it is gathered in the steam vessel, typically positioned atop the boiler. Through a network of pipes, the steam can then be directed to its intended destination, whether it be for powering mechanical equipment, heating systems, or industrial processes.
- Venting of flue gases: As fuel combusts, releasing heat energy, flue gases and exhaust gases are produced and expelled through a designated flue system. The flue, comprising passages, channels these gases into the atmosphere. Within the flue system, additional components like flue gas cleaners are frequently incorporated to mitigate the emission of pollutants from the exhaust gases.
The workflow of an industrial steam boiler is a continuous cycle of fuel combustion, heat transfer, heating and conversion of water to steam, collection and distribution of steam, and flue gas emissions. The process is designed to efficiently convert the energy of the fuel into usable steam energy to meet the power, heating and control needs of industrial production. At the same time, through proper design and operation, industrial steam boilers can achieve energy savings and environmental protection.
The maintenance and safety of industrial steam boilers is an important aspect of ensuring their reliable operation and the safety of employees.
- Regular maintenance and servicing: Maintaining and servicing steam boilers is crucial to ensure their proper operation. This involves routine cleaning of various components, inspecting and replacing damaged parts, and conducting systematic inspections and tests. Regular maintenance helps identify and address potential issues, prolonging the boiler's lifespan and enhancing operational efficiency.
- Safe operating practices: Ensuring the safe operation of steam boilers is paramount. Operators must undergo professional training on the boiler's operating procedures and safety protocols. Familiarity with operational requirements, including start-up and shut-down procedures, combustion control, water level control, and pressure control, is essential. Strict adherence to these requirements significantly mitigates the risk of accidents and operational errors.
- Compliance requirements: Industrial steam boilers must be operated in accordance with relevant regulations and standards. These regulations and standards may cover requirements for the design, installation, operation and maintenance of the boiler. Companies should be aware of and comply with relevant national, regional and industry regulations to ensure boiler compliance, and carry out the necessary audits and permits.
- Testing and monitoring: Boilers should be outfitted with suitable testing and monitoring equipment to continuously track their real-time operational status. This equipment may encompass water level controls, pressure gauges, thermometers, and combustion controls. The monitoring of crucial parameters allows for the prompt detection of abnormalities, enabling timely intervention to ensure the safe operation of the boiler.
- Staff training and awareness-raising: Beyond regular maintenance and operational safety measures, it is crucial to prioritize training and enhance the safety awareness of staff. Employees should be well-versed in the fundamental working principles, safe operating procedures, and emergency measures related to boilers. Organizing regular training courses and safety drills helps improve employees' knowledge and readiness to respond effectively to boiler safety concerns.