The textile printing industry, known for its vibrant colors and intricate designs, heavily relies on efficient and reliable equipment. One crucial component that often goes unnoticed but plays a pivotal role in ensuring quality and productivity is the boiler system. This article delves deep into the world of boilers for textile printing, providing insights into their significance, operations, and selecting the right type for optimal performance.
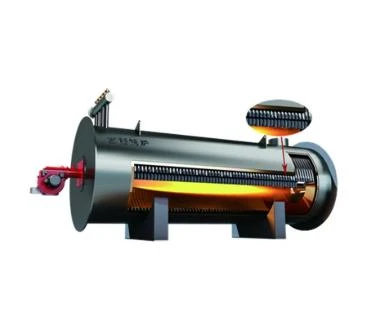
Boilers serve as the powerhouse of the textile industry, providing the necessary steam that is crucial for various printing processes. The steam generated by these boilers is used for transferring vibrant colors and patterns onto fabrics, ensuring they adhere properly and produce long-lasting results. Moreover, these machines aid in the setting of dyes and pigments, offering stability and consistency in the final product.
One of the most common types of boilers used in textile printing is the steam boiler. Its ability to maintain consistent temperature and pressure is essential for achieving uniform prints. Steam boilers are valued for their efficiency and durability, making them a staple in textile manufacturing plants. Their design allows for quick heating, reducing downtime and enhancing productivity, which is a significant advantage in high-demand production environments.
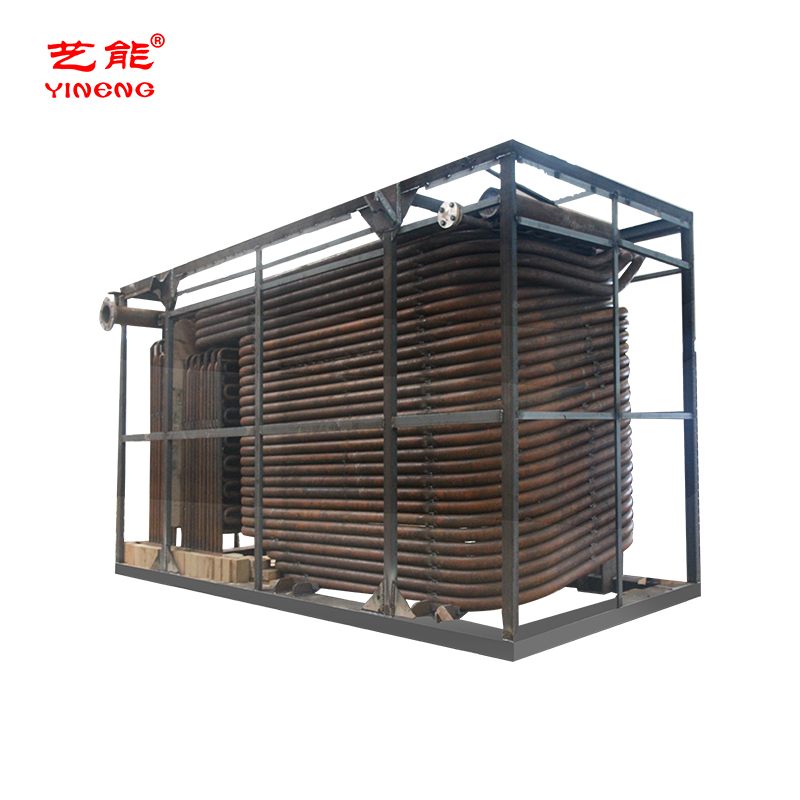
When choosing a boiler for textile printing, several factors must be considered. Firstly, the size of the production facility and the volume of output directly influence the type of boiler required. Large-scale operations may benefit from industrial-sized boilers capable of handling extensive fabric lengths and continuous operation. In contrast, smaller workshops might opt for compact models that offer flexibility and ease of maintenance.
boiler for textile printing
Energy efficiency is another critical factor. With environmental concerns and cost efficiency driving industrial innovations, many manufacturers are opting for eco-friendly boilers. These modern systems utilize advanced technology to reduce fuel consumption and optimize energy use, translating to lower operational costs and a reduced carbon footprint. The integration of renewable energy sources in boiler operations is also gaining traction in the textile industry, reflecting a shift towards sustainable practices.
Safety and reliability are paramount. Boilers must adhere to strict safety regulations to prevent accidents that could jeopardize the workforce and the facility. Regular maintenance checks and quality certifications are essential to ensure that boilers operate smoothly and safely over their lifespan. Automated controls and monitoring systems are becoming increasingly popular, offering real-time data and alerts to avert potential issues before they escalate.
Partnership with reputable boiler manufacturers and service providers can also enhance the reliability and efficiency of the operations. Industry-leading suppliers often offer comprehensive solutions, including installation, maintenance, and troubleshooting services, ensuring that textile printing businesses maintain optimal operations without unexpected interruptions.
In conclusion, the boiler system is an indispensable asset to the textile printing industry. Its role in producing high-quality prints and maintaining efficient operations cannot be overstated. By prioritizing energy efficiency, reliability, and safety, businesses can ensure their boiler systems align with technological advancements and environmental standards. As the industry evolves, so too must the equipment, ensuring it meets the demands of modern textile production while paving the way for sustainable practices. The careful selection and management of boiler systems will undoubtedly provide textile printers with a competitive edge in an increasingly dynamic market.