When it comes to optimizing efficiency and performance in industrial applications, selecting a high-quality steam boiler heat exchanger is paramount. The steam boiler heat exchanger serves as a critical component that impacts both operational costs and energy consumption. Here, we delve into the characteristics that define top-tier steam boiler heat exchangers, ensuring industries across the board can harness their full potential.
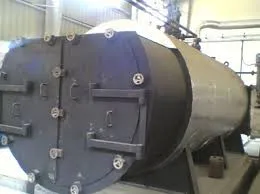
A steam boiler heat exchanger's effectiveness largely hinges on its construction material. High-grade alloys such as stainless steel and Inconel provide unparalleled resistance to corrosion and thermal expansion. Stainless steel, in particular, stands out due to its ability to maintain integrity and performance under high-temperature and high-pressure conditions. With the addition of chromium, stainless steel forms a passive layer that protects against oxidation and extends the lifespan of the heat exchanger. These features not only enhance the durability but also contribute to a safer operational environment, ensuring optimal heat transfer over prolonged periods.
The design of a steam boiler heat exchanger significantly influences its heat transfer efficiency. One cutting-edge design is the compact, shell-and-tube configuration, which facilitates maximum surface area for heat exchange while minimizing spatial requirements. This design utilizes a series of tubes, where steam passes through the shell side and the coolant flows through the tubes, or vice versa. Such innovative configurations optimize the turbulence of fluid flow, enhancing heat transfer efficacy while reducing fouling and deposits, a frequent cause of inefficiencies and maintenance downtime. Moreover, the modular design of these exchangers allows for ease of maintenance and scalability, accommodating evolving industrial needs without significant overhaul.
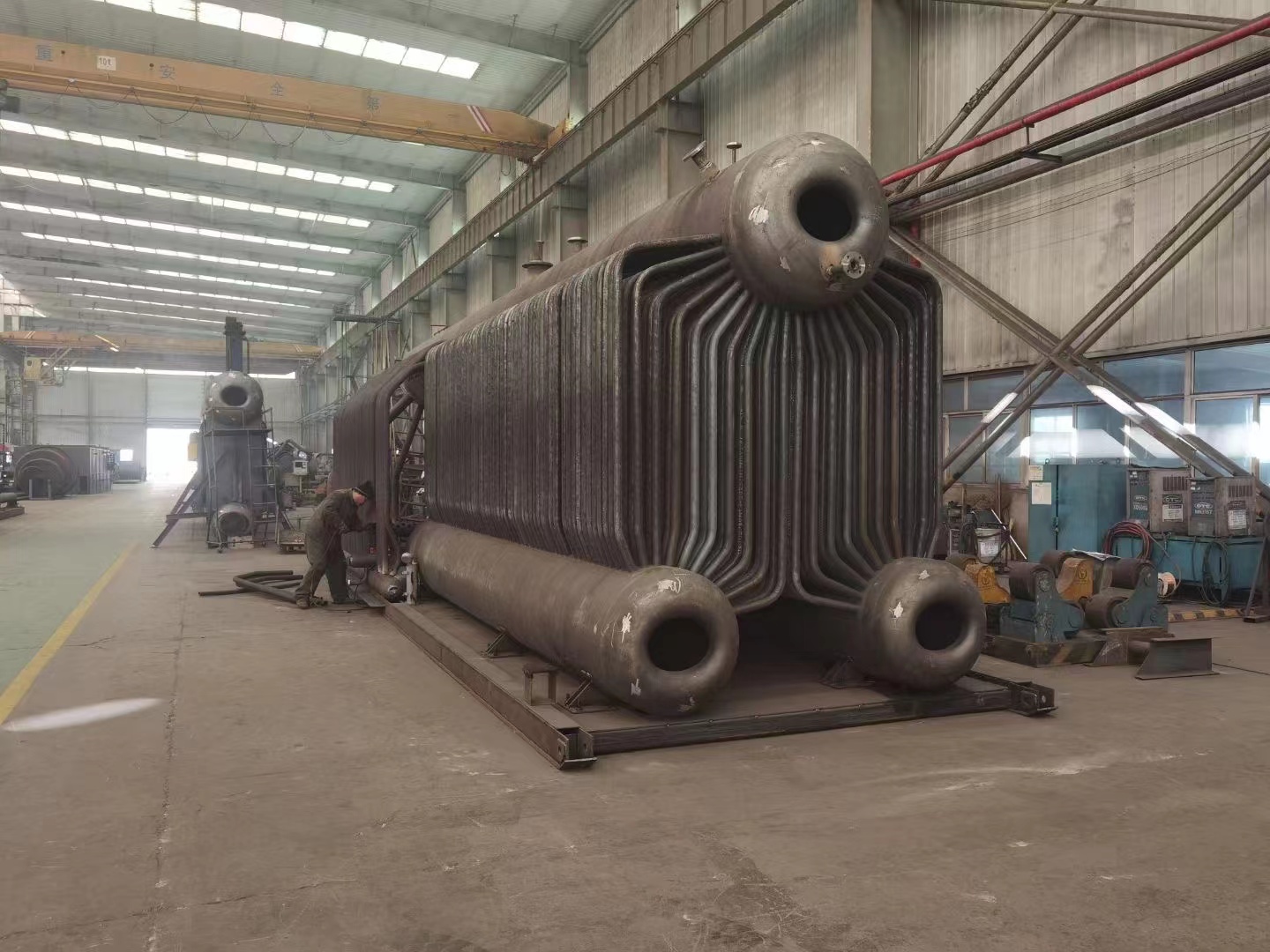
Efficiency in steam boiler heat exchangers isn't solely dependent on mechanical design; advanced surface treatments also play a critical role. Cutting-edge technologies allow for the application of specialized coatings that reduce friction and improve thermal conductivity. These coatings inhibit deposit formation, thus maintaining a consistently high rate of heat transfer and extending intervals between maintenance checks. For instance, Teflon-based coatings provide a non-stick surface that enhances fluid dynamics and operational efficiency.
high quality steam boiler heat exchanger
Ensuring compliance with international standards and certifications such as ASME, CE, and ISO demonstrates the reliability and safety of a steam boiler heat exchanger. These certifications are not mere formalities; they guarantee that the exchanger has undergone rigorous testing for pressure resistance, environmental compatibility, and safety performance. Industrial leaders seeking to assert their commitment to quality and safety prioritize equipment that bears these trusted seals of approval.
Another distinguishing factor of high-quality steam boiler heat exchangers is their energy consumption efficiency. With rising global awareness of energy conservation, industries are under pressure to minimize their carbon footprint. State-of-the-art heat exchangers incorporate features like feedwater economizers and condensing technology to reclaim heat that would otherwise be wasted, yielding significant reductions in fuel consumption and emissions. Such innovations align with sustainability objectives, making them an invaluable asset for companies aiming to adhere to environmental regulations while reducing operational costs.
Finally, continuous monitoring and smart integration are hallmarks of modern steam boiler heat exchangers. The implementation of IoT sensors embedded within the unit provides real-time data on performance metrics such as temperature differentials, flow rates, and pressure drops. This facilitates predictive maintenance and immediate troubleshooting, thus minimizing downtime and maximizing productivity. Integration with digital management systems allows operators to make data-driven decisions that enhance both short-term operations and long-term strategic planning.
In selecting a high-quality steam boiler heat exchanger, one must consider factors that not only meet immediate heating requirements but also offer robust returns on investment through efficiency, safety, and longevity. Through leveraging advanced materials, cutting-edge designs, and adherence to stringent standards, industries can ensure they are equipped with the finest technology to support their operational excellence and sustainability goals. Such informed decisions lead to enhanced credibility and establish a leadership stance in an increasingly competitive global market.