The global demand for steam generation systems is accelerating, with electric steam boiler manufacturers leading innovation in energy efficiency, emission reductions, and process automation. In this comprehensive analysis, we cover technical trends, product specs, process diagrams, and application scenarios—comparing mainstream products and manufacturers. Whether in heavy industry, pharmaceuticals, or food processing, the right steam boiler is critical for operational safety and economic efficiency.
1. Industry Trends Among Electric Steam Boiler Manufacturers
- Decarbonization: Organizations seek electric or high-efficiency gas steam boiler for sale solutions to comply with stricter emissions regulations.
- Digitalization: Integration of IoT and SCADA in steam boiler industrial setups elevates automation, remote monitoring, and predictive maintenance.
- Material Innovation: Advanced alloys and anti-corrosive linings, such as duplex stainless steel, significantly extend service life and reduce maintenance.
- Customization: Shift towards tailored solutions—water tube steam boiler variants, heat exchanger upgrades, and custom thermostat for steam boiler controls.
Key Statistical Overview (2024)
- Global industrial steam boiler market was valued at $17.9 billion in 2023 (Source).
- Electric steam boiler manufacturers are projected to grow at a CAGR of 7.2% (2024-2030).
- 50%+ of new enquiries for steam boiler industrial solutions mandate ISO 9001 and ANSI/B31.1 compliance.
2. Manufacturing Process of Electric Steam Boiler Manufacturers
(Duplex Stainless Steel, Alloy Steel)
(Cutting, Casting, Forging, CNC Machining, Welding)
(Steam boiler heat exchanger, sensors, controls)
(Hydrostatic, Radiographic, ISO/ANSI certified)
(Site installation, Warranty Service)
The backbone of electric steam boiler manufacturers is rigorous material selection—premium duplex stainless steel ensures resistance against scaling, pitting, and corrosion during high-pressure operation. Core components undergo forging and precision CNC machining, resulting in exceptional dimensional accuracy and structural integrity. All boilers are subjected to hyper-strict hydrostatic tests (per ISO 16528-1) and radiographic weld checks (per ANSI/ASME Section VIII).
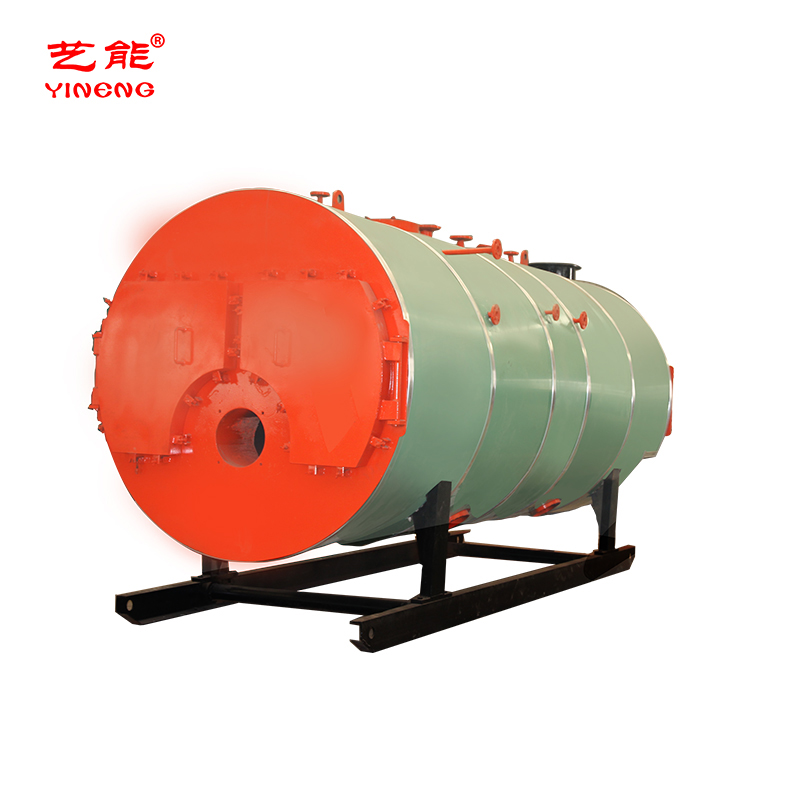
Materials & Processes
- Steel Plate, Tubing: ASTM A516 Gr. 70 / A335 / EN 10028 grade
- Welding: TIG, MIG, Robotic Submerged Arc with post-weld heat treatment
- Casting: Manifolds, pressure vessel collars (vacuum casting)
- Machining: CNC lathing — achieves ±0.02 mm tolerance
- Non-Destructive Testing (NDT): Magnetic, Dye Penetrant, Ultrasonic
- Service Life: 15–25 years with regular maintenance
3. Product Data & Technical Comparison Among Leading Electric Steam Boiler Manufacturers
Manufacturer | Model | Firing Method | Materials | Power Output (kW/t) | Steam Pressure (MPa) | Efficiency | Certifications | |
---|---|---|---|---|---|---|---|---|
Thermal | Electrical | |||||||
Yongning Boiler | WNS Series | Gas/Oil/Electric | Q245R, 304/316L SS | 700~28000 | 0.7-2.5 | 98.4% | 97.2% | ISO9001, CE, SGS |
Electro Industries | EB72-3 | Electric | Alloy steel/SS | 500~12000 | 0.4-1.6 | 99% | 99.4% | UL, CSA |
Weil McLain | EG 40 Steam | Gas/Atmospheric | Cast Iron, Carbon Steel | 1155 | 0.86 | 84% | – | ASME, AHRI |
Fulton Boiler | VSRT-250 | Gas/Electric | Duplex SS, Alloy Tube | 250~4000 | 1.0-2.5 | 99.5% | 98.0% | UL, CE, ISO14001 |
Simons Boilers | SB Electric | Electric | SS 304, 316 | 500~1500 | 1.0 | 99% | 98.7% | AS ISO 9001 |
Key: Thermal Efficiency relates to combustion process, Electrical Efficiency is power-to-steam yield (electric boilers). Pressure values in MPa.
Trends by Region (Market Share in %)
4. Product Spotlight: Gas oil fired WNS series automatic hot water boiler
- Structure: Horizontal, wet-back, three-pass fire tube
- Fuel Type: Natural gas or light oil (optional biomass/syngas)
- Thermal Efficiency: Up to 98.4% (EN12952:2014 tested)
- Capacity: 0.7MW–28MW (1,000–40,000kg/h steam)
- Max Pressure: 2.5 MPa (GH300–GH2800 models)
- Emissions:
- Controls: PLC+HMI, Wi-Fi/4G remote monitoring
- Warranty: 18 months core, 15 yrs shell
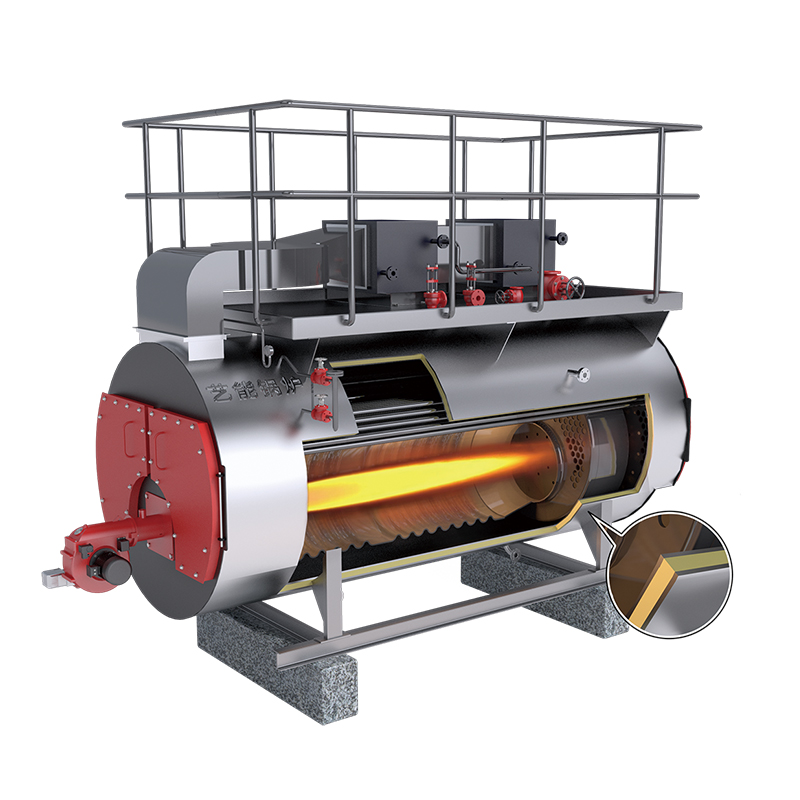
Key Specifications - Gas oil fired WNS series automatic hot water boiler | |
---|---|
Rated Output | 0.7–28 MW (steam)/1–40 t/h (steam) |
Design Pressure | 0.7/1.0/1.25/1.6/2.5 MPa |
Thermal Efficiency | Up to 98.4% |
Boiler Body Material | Q245R Carbon Steel, 304/316L Stainless Steel tubes |
Burner | Bentone/Weishaupt/Riello/Customized |
Control System | Siemens/Schneider PLC+Touchscreen HMI |
Applicable Standards | ISO9001, EN12953, CE, ASME |
Typical Applications | Petrochemical, Textile, Food Processing, Water Treatment, Pharma |
5. Manufacturer Comparison & Customization Services
Aspect | Yongning WNS Series | Wood Steam Boiler | Water Tube Steam Boiler | Weil McLain EG 40 |
---|---|---|---|---|
Max Pressure | 2.5 MPa | 1.25 MPa | 3.2 MPa | 0.86 MPa |
Material | Q245R, 304/316L SS | Cast iron, firebrick | Duplex SS/alloy (ASTM A335) | Cast iron |
Efficiency | Up to 98.4% | 80–84.5% | 97.5% | 84% |
Emission Control | Ultra-low NOx/CO | Manual, high PM | Automated, low particulate | Legacy (no advanced control) |
Automation | PLC/HMI, IoT ready | Manual/Basic | Full automation, IIoT | Basic mechanical |
Applications | Industrial/Commercial | Agriculture, rural | Petro/Refineries | Residential-Commerc. |
6. Customization and Engineering Solutions
- Full modularity: multiple steam boiler industrial units in cascade
- Custom heat exchangers for high-salinity water, aggressive media
- Third-party compliant thermostat for steam boiler systems (CE, ISO, UL listed)
- Emission solution upgrade (SCR, ultra-low NOx cap
- Remote operation dashboards (cloud-linked)
Standard models: 20–30 days. Custom engineered: 6–12 weeks depending on options and compliance.
Warranty: 18 months full (24/7 support), 15 years shell defect guarantee.
7. Application Scenarios & Case Studies
Petrochemical Refinery (Asia-Pacific)
- Installed: 3 x 15t/h electric steam boiler manufacturers WNS series boilers
- Savings: Reduced fuel cost by 18%, cut water chemistry failures by 37% (ISO9001 monitored O&M)
- Integration: DCS/PLC, real-time steam demand optimization
Pharmaceutical Cleanroom (Europe)
- Compact 1.5t/h gas steam boiler for sale, EN12952 pressure rating
- Result: GMP sterile compliance, 21.3% reduction in CO₂ (test: TÜV SÜD Germany)
Municipal Wastewater (North America)
- Installed: Steam boiler heat exchanger system for sludge treatment
- Uptime: 99.7% annual, ROI achieved in 26 months
8. Professional FAQ – Electric Steam Boiler Manufacturers Industry
- Q: What is the expected lifetime of an electric or gas steam boiler industrial system?
A: With corrosion-resistant materials (duplex steel, 316L), and per ISO 16528-1 certification, 15–25 years is typical for industrial-scale installations. Regular NDT and chemistry checks are essential. - Q: How are thermostat for steam boiler controls integrated?
A: Typically, digital thermostats interface with a PLC (Programmable Logic Controller), using PT100 RTD sensors. They maintain ±0.5°C accuracy on output temperature. - Q: Which standards do leading electric steam boiler manufacturers comply with?
A: ISO 9001, EN12952/53 (EU), ASME Section I & VIII (US), CE, and CSA for North America. ANSI B31.1 ensures safe pressure vessel operation. - Q: Which materials are best for steam boiler heat exchanger durability?
A: Stainless steel (316L, duplex), Incoloy for aggressive/acidic feeds. Alloy selection (ASTM A335 for tubes, Q245R for shells) determines longevity. - Q: How are water tube steam boiler and fire tube boilers different?
A: Water tube boilers operate at higher pressures (>3MPa), transfer steam quicker, and are used in heavy industry. Fire tube designs (like WNS) are more efficient for low to mid-pressure streams. - Q: Can gas steam boilers for sale be retrofitted with emission controls?
A: Yes. SCR (Selective Catalytic Reduction), FGR (Flue Gas Recirculation), low-NOx burners, and economizers can be retrofitted for NOx/SOx/CO control to comply with new emission legislations. - Q: What are typical installation and inspection protocols?
A: Factory Acceptance Test (FAT), hydrostatic pressure test (usually at 1.5x design pressure), radiographic weld inspection, UL/CE marking, and local regulatory (city or state-level) inspection prior to commissioning.
9. Customer Support, Delivery, and After-Sales Service
- Full project consultancy with 3D design previews and site simulation
- On-site supervision, certified installation, and hands-on O&M training
- Round-the-clock technical hotline (response within 2 hours)
- OEM and branded spare parts inventory management (10 years+)
- Cloud-based support portal: logs, self-diagnostic tools, user manuals
10. References and Authoritative Industry Resources
- Grand View Research. (2023 Industrial Boilers Market Report)
- ASME Boiler and Pressure Vessel Code (Section I)
- ISO 16528-1: Boilers and Pressure Vessels Standard
- HeatingHelp.com forum discussion – Electric vs Gas Steam Boiler Manufacturers
- ScienceDirect – "Life cycle and cost benefit analysis of steam boiler industrial projects" (Full Text)